El templo de Xsara y Picasso
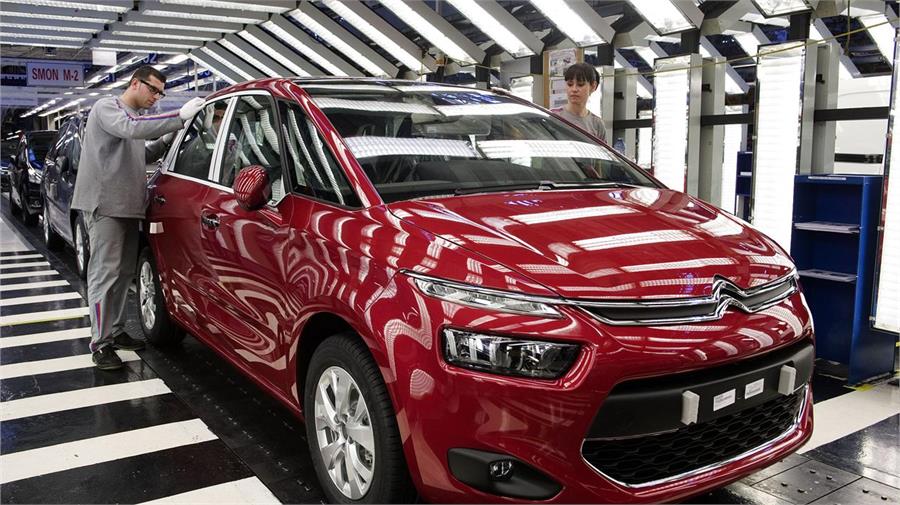
Ayer tuvimos la suerte de visitar la planta de PSA (Peugeot-Citroën) de Balaídos, en Vigo, invitados por Citroën. Una planta cuyo enfoque organizativo está dando unos excelentes resultados y que está, tras años de trabajo e investigación, a punto de cuantificar sus éxitos, de recoger su cosecha.
La planta, con un corazón movido por unos 7.000 empleados, está en condiciones de aumentar este año un 33% su producción. Dicho de otro modo, fabricar 400.000 vehículos al año sin estar al máximo de la capacidad de producción; más de 1.750 vehículos al día, o en algunos puntos llegar a fabricar un coche al minuto –esta ratio se da concretamente en la línea de montaje número 1 dónde se realizan tres turnos y se trabaja seis días a la semana y siete noches-. De allí salen para todo el mundo los vehículos comerciales, Citroën Berlingo y Peugeot Partner, y los coches ‘low cost’, C-Elysée y Peugeot 301. El 88% de la producción se exporta.
La línea número dos, en la que se hacen los monovolúmenes, no tiene un ritmo tan frenético. Llegarán al final del verano a 40 unidades a la hora. Por la noche, la línea está inactiva y esa franja horaria libre parece estar llamando a gritos a todo Vigo: “¡¡Aquí puede haber más trabajo!!”. En palabras del director de la fábrica, Juan Antonio Muñoz Codina, “la ampliación de la plantilla solo podría ligarse a una buena acogida mundial del C4 Picasso”.
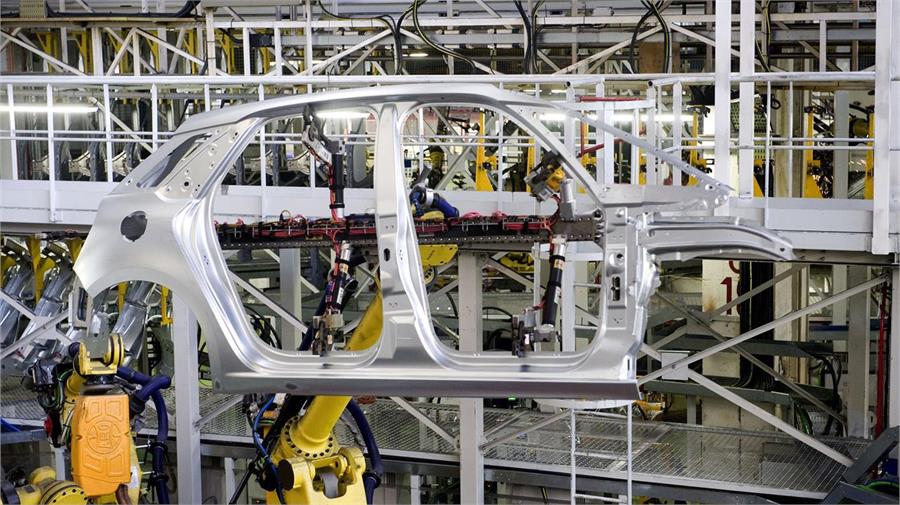
Todo ello se me antoja que es como la visita a un templo o al menos a un espacio sagrado dónde aún perdura una vieja creencia: trabajo más ingenio más ajustes laborales más inversión, siempre es igual a prosperidad. Y esta sagrada fórmula vence incluso a una crisis rabiosa.
Los empleados, además de hacer posible el logro, han recortado algunas de sus primas o ventajas laborales. También han estado a la altura de las circunstancias. Todo ha colaborado en esta punta del mundo a que la máquina funcione perfectamente engrasada, lista para recibir más de 1.000 millones de euros de inversión de su Grupo (para la creación de los sedanes Citroën C-Elysée y Peugeot 301 y la fabricación de las versiones eléctricas de la Partner y la Berlingo).
Optimización de recursos
PSA Vigo ha sabido plasmar en los últimos años las estrategias necesarias para llegar al punto actual. Tenía varios focos a resolver. A partir de su localización y el tamaño de sus instalaciones ha tenido que jugar a optimizar recursos, espacio y tiempo.
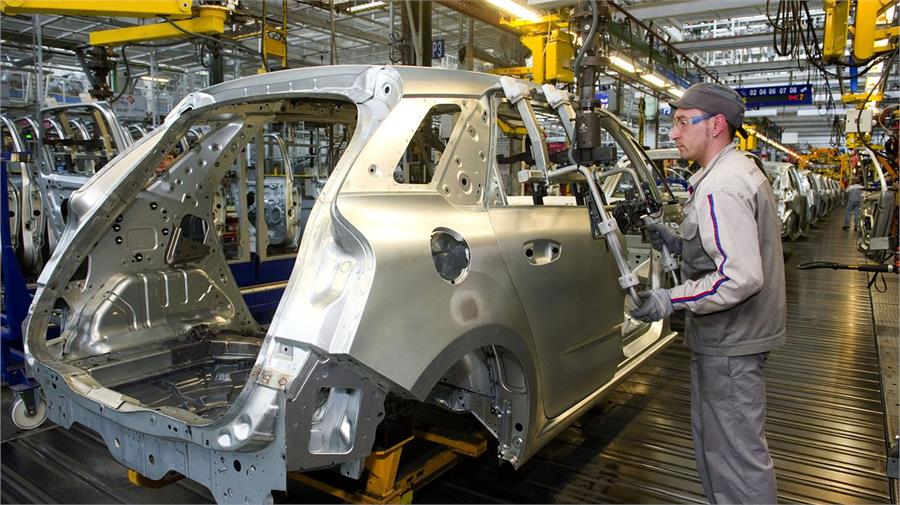
El trabajo coordinado con los proveedores -más de 100 empresas del sector están ubicadas en el área de Vigo- y con otras filiales del Grupo como la planta portuguesa de Mangualde, han hecho posible la optimización del tiempo.
También se han aplicado soluciones en una zona de la cadena que permite ensamblar laterales del vehículo en un espacio circular o en hélice, lo que reduce la superficie de trabajo. El espacio físico que libera este dispositivo es de 11.000 metros cuadrados, una ganancia que en una planta compacta como la de Vigo es importante. Este proceso llamado “Heliflexor” también es una aportación gallega al Grupo, es otra muestra del carácter pionero de la fábrica.
La racionalización de procesos con soluciones inteligentes es una de las mejores cartas de presentación de esta planta ante el resto del Grupo PSA.
Suscríbete a la newsletter
Si quieres estar al día de nuestras noticias, tienes que tener una cuenta en coches.net.
Dominar la masa

Pero si ha habido un paso importante en la filial ha sido, sin duda, la fabricación de la nueva plataforma modular para vehículos, la EMP2. Aunque oficialmente solo se monta en el Picasso (dos versiones) ya se está construyendo para más coches del Grupo, como el Peugeot 308.
Esta plataforma, que podría emplearse en el futuro en el 50% de los modelos del Grupo –los que miden entre 4 y 5 metros– se ha empezado a montar en Balaídos, y ya se empieza a instalar en el 308, en Francia.
Dos objetivos ha cumplido esta plataforma: la reducción de peso del vehículo y la reducción de costes de fabricación.
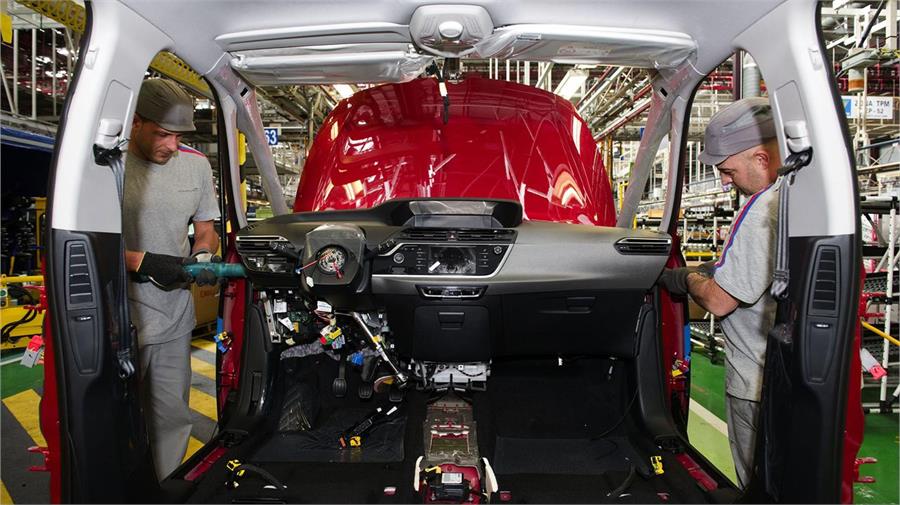
La plataforma es tan polivalente que es compatible con gran cantidad de modelos. A partir de un bloque delantero único se acopla a numerosos tipos de traseras: más cortas, más largas, diversas posiciones de conducción (más altas, más bajas), distintos tipos de trenes traseros y diferentes mecánicas. Da 4 opciones de ancho de vía delantero y 5 alternativas de distancia de ejes.
El director de la planta, Juan Antonio Muñoz Codina, comentó que con tan solo una plataforma más, de diferente longitud, se cubrirá la totalidad de modelos del Grupo.
El otro objetivo cumplido es el dominio de la masa. La plataforma supone un ahorro de peso de 70 kg en el modelo final. Permite procesos de fabricación avanzada como la estampación en caliente, las chapas de espesor variable, el hidroformado y las soldaduras laser. Además permite emplear materiales en la fabricación del coche que rebajan mucho el peso como el aluminio, el composite o el acero de alta resistencia.
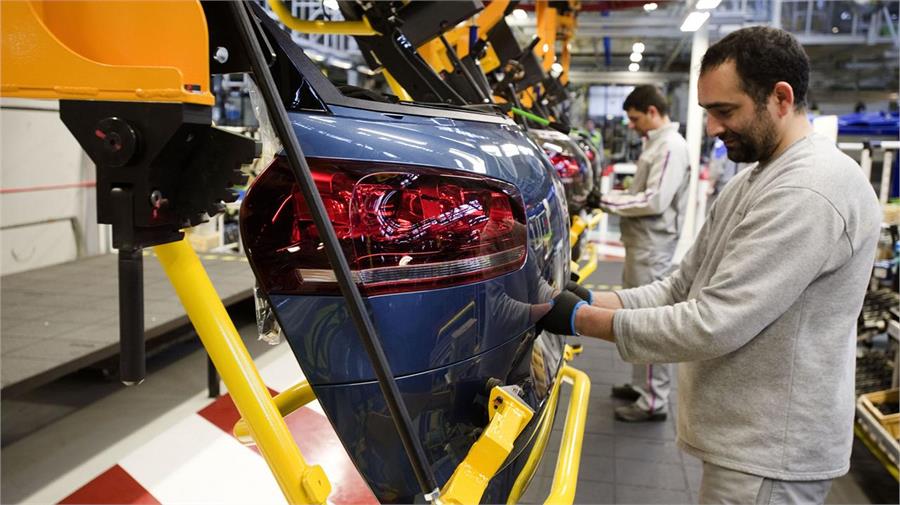
Todo ello ha propiciado que el nuevo C4 Picasso y su versión de 7 plazas, el Grand C4 Picasso –con nuevo portón trasero hecho de composite- pese 140 kg menos que otras generaciones anteriores. Así no es difícil mejorar las prestaciones del vehículo. El trabajo previo de dominio de la masa ha sido vital. Los Picasso son un hito que consolidan esta fábrica gallega pero de las paredes de la factoría cuelgan recuerdos de coches que nos acompañaron mucho tiempo. Millones de unidades de modelos como el 2CV, el Mehari, el Dyane 6, el C-15, el 504 y el 505, los ZX o los Xsara se han ensamblado desde 1958 en este rincón del mundo.
Yo tengo trabajo gracias al nuevo c4 picasso, fabrico el porton trasero de composite y el fondo del maletero, espero que sea un éxito de ventas jejejeje